South-Tek
Design Elements
Sample Page
Headings
Inter Typeface
If you rely on nitrogen, rely on a South-Tek Systems nitrogen generator.
If you rely on nitrogen, rely on a South-Tek Systems nitrogen generator.
If you rely on nitrogen, rely on a South-Tek Systems nitrogen generator.
If you rely on nitrogen, rely on a South-Tek Systems nitrogen generator.
If you rely on nitrogen, rely on a South-Tek Systems nitrogen generator.
If you rely on nitrogen, rely on a South-Tek Systems nitrogen generator.
Paragraphs
Inter Typeface
The BeerBlast system generates beverage grade nitrogen safely and efficiently from the air. South-Tek Systems’ Mixed Gas Dispense System redefines Nitrogen generation technology for draft beer applications. Engineered for greater longevity and higher output, the BeerBlast provides the exact blend of carbon dioxide (CO2) and Nitrogen (N2), protecting the kegged product quality – ultimately increasing profitability and customer satisfaction. The internal gas blender mixes the Nitrogen with CO2 for precise CO2/Nitrogen blends of 70/30 or 60/40, and 25/75 (or any ratio desired). When it comes to reliability, BeerBlast’s dual-bed PSA technology is first-in-class, ensuring that you will never run out of nitrogen when it matters most.
Over- and under-carbonation can affect the quality and taste of beer. In addition, they both lead to a loss in revenue and customer satisfaction. The BeerBlast System helps establishments provide the highest quality beer, while minimizing waste and recuperating revenue loss.
Over-carbonation can occur when pushing beer with either 100% CO2 or an incorrect mixed gas ratio. This can result in a “foamy pour” which will either leave the customer unsatisfied with their pint or the bartender will continue to pour the foam out and refill the glass until the desired level of foam is reached. Even worse, the wrong blend can actually ruin the contents in the keg. Up to 20% of the beer that should be sold to customers will turn to foam and remain in the keg when it heads back to the wholesaler!
Colors
Black
Light Blue
Dark Blue
Yellow
Red
Green
CTAs
Icons
Industrial
Metals
Food &
Beverage
Fire
Protection
- Food & Beverage
BrewBlast
Mission-Critical Nitrogen™ BrewBlast Nitro Gas Dispense System
The BrewBlast Nitro Gas Dispense System is designed specifically for mission-critical nitrogen™ infused cold brew coffee applications. Engineered with the most efficient nitrogen gas separation technology and the smallest available footprint, BrewBlast produces ultra-pure nitrogen gas for pouring cold brew coffee. Generate nitrogen on-demand and ensure your cold brew tastes just as the brewer intended.
Mission-Critical Nitrogen™ BeerBlast Mixed Gas Dispense System
The BeerBlast system generates beverage grade nitrogen safely and efficiently from the air. South-Tek Systems’ Mixed Gas Dispense System redefines Nitrogen generation technology for draft beer applications. Engineered for greater longevity and higher output, the BeerBlast provides the exact blend of carbon dioxide (CO2) and Nitrogen (N2), protecting the kegged product quality – ultimately increasing profitability and customer satisfaction. The internal gas blender mixes the Nitrogen with CO2 for precise CO2/Nitrogen blends of 70/30 or 60/40, and 25/75 (or any ratio desired). When it comes to reliability, BeerBlast’s dual-bed PSA technology is first-in-class, ensuring that you will never run out of nitrogen when it matters most.
N2Blast: Mission-Critical Nitrogen™ Generators for Dry Fire Protection Systems
The N2Blast Corrosion Inhibiting System is designed to protect fire protection sprinkler systems from corrosion and extend system life. The N2Blast nitrogen generator introduces up to 98.5%+ pure nitrogen into the dry or pre-action fire protection system and displaces oxygen, a key contributor to the corrosion reaction, using the AutoPurge System. The N2Blast effectively inhibits Electrochemical, Galvanic and Microbiologically Influenced Corrosion (MIC), as well as sprinkler pipe ice plugs.
Frequently Asked Questions
Got a question?
We are here to answer.
- Last updated: March 2023
- Power down the unit and confirm that the pressure reading on the gauge above the filters reads 0 PSI.
- Disconnect the drain lines from the filter bowls by pushing the orange rings towards the filter bowl, while pulling down on the poly lines.
- Unscrew the filter bowls by hand by rotating the outer metal casing clockwise.
- Pull down on the plastic filter bowls to remove them from the upper filter housing taking care to remove the O-rings. The O-rings can be discarded.
- The black filter element on the left can be removed from the upper filter housing by rotating clockwise and discarded.
- The white filter element on the right can be removed from the plastic filter bowl by gently prying up on the black upper filter assembly with the O-ring removed. Once removed from the filter bowl, rotate the lower piece of the filter assembly a quarter turn counter clockwise. The white element can be discarded and replaced and then reassembled.
- Fill the plastic filter bowl about half way with warm soapy water and shake with your hand covering the top opening. Repeat for both bowls. This will ensure that the float drain is clean and operational.
- Remove and replace the O-rings on the lip of the plastic filter bowl.
- Install the outer metal casing back onto the plastic filter bowl, taking care to line up the protrusion on the bottom with the opening in the metal casing.
- Reinstall the filter housing and casing back into the upper filter assembly. Only tighten hand tight and do not use a wrench.
- Reinstall the poly drain lines by pushing up into the bowl until the push to connect fitting locks the line into place.
- The compressor intake filter can be replaced by pushing down on the black filter bowl located on the top of the compressor and rotating counter clockwise. Take care that the filter housing may be hot.
- Turn on the unit and test for any leaks with a a spray bottle and soapy water.
- Reset the filter alarm by holding the Down (-) key on the controller for 10-15 seconds.
It is recommended that your analyzer be checked for accuracy on an annual basis. If your calibration is off or is reading incorrectly, then follow the steps below for recalibration. To verify the accuracy of your analyzer, simply connect the sample line to a cannister of known test gas and ensure that the reading on your controller screen matches the test gas. Quotes for test gas can be requested via support@southteksystems911.zendesk.com or (910) 415-1880.
- Turn generator off.
- Close the ball valve connected to sample line at N2 storage tank.
- Disconnect sample line from outside of electrical cabinet.
- From the PLC (display) on the generator:
- Press “Menu”
- Enter Password (6557) and press the bottom right button (return key).
- Select “sensor setup/calibration.”
- Select “O2 PPM/% calibration”
- For % Units:
- Enter the contents of your known gas source in the field labeled “0-2% O2 Calibration Gas.” This will be listed on the Test Gas cannister and is typically 1%.
- Enter 20.9% in the field labeled “20-22% O2 Calibration Gas.”
- For PPM units:
- Enter the contents of your highest purity (lower PPM) known gas source in the field labeled “O2 PPM Low Calibration.” This will be listed on the Test Gas cannister and is typically 10 PPM.
- Enter the contents of your lowest purity (higher PPM) known gas source in the field labeled “800-1000 PPM Cal Gas.” This will be listed on the Test Gas cannister and is typically 700 PPM.
- Connect the provided regulator onto your higher purity (10 PPM) known gas source.
- Connect the provided tubing over the sample line connector on the electrical cabinet.
- Open the valve on the regulator and allow gas to flow to the analyzer for minimum of 5 minutes.
- On the PLC there is a value displayed at the bottom of the calibration screen labeled “Current Raw”.
- Take the “current raw” value and enter it in the top field (low side calibration)
- Close the valve on the regulator.
- Switch the regulator to your high side calibration gas.
- Open the valve and allow gas to flow for 5 minutes.
- On the PLC there is a value displayed at the bottom of the calibration screen labeled “Current Raw”.
- Take the “current raw” value and plug in the 2nd field (high side calibration)
- Close the valve on the regulator.
- On the PLC there is a value displayed at the bottom of the calibration screen labeled “Current Raw”.
- Disconnect the tubing from the sample port.
- Reconnect your sample line to the sample port.
- Open the valve on the storage tank feeding the sample line.
- On the PLC there is a value displayed at the bottom of the calibration screen labeled “Current Raw”.
- For % Units:
This should complete calibration on your analyzer. If you have trouble or require assistance, please give us a call at 910-415-1880.
Fire Protection
N2-Blast Filter Kit
FPS-250, 250FF, 500, 750, 750FF, 900, 1650 | FRP-007 |
FPS-1750, 3000, 6000 | FRP-002 |
FPS-12000, 15000, 18000, 20000, 22500 | FRP-006 |
FPS-3250, 5000, 10000 (BLACK FILTER BOWLS) | FRP-013 |
FPS-3250, 5000, 10000 (WHITE FILTER BOWLS) | FRP-022 |
POWER SAVER MANIFOLD | 100692 |
QUICK CHECK PURITY MANIFOLD | 100692 |
MIC Blast Filter Kit
FPS-20, 50 | FRP-007 |
FPS-125, 200, 400 | FRP-002 |
FPS-2000, 3000 | FRP-006 |
Beverage
1KPH, 3KPH, 7KPH, 14KPH | FRP-001 |
100, 200 | FRP-003 |
400 | FRP-004 |
100, 200, 400 PLUS | FRP-001 |
600, 800 PLUS | FRP-005 |
Labtek
35L, 30D | FRP-015 |
70T | FRP-017 |
70L, 90D | FRP-016 |
Tire Blast
NT-10, NT-20, NT-40 | FRP-009 |
NT-130, NT-250 | FRP-008 |
Transmissions Lines
TL-450, TL-1050, TL-1825 | FRP-007 |
TL-1725, TL-2625 | FRP-010 |
Please reach out to the email or phone number below for quotes on any of the above, or if you do not see your particular N2 generator listed.
support@southteksystems911.zendesk.com
910-415-1880
- Power down the unit and confirm that the pressure reading on the gauge above the filters reads 0 PSI.
- Disconnect the drain lines from the filter bowls by pushing the orange rings towards the filter bowl, while pulling down on the poly lines.
- Unscrew the filter bowls by hand by rotating the outer metal casing clockwise.
- Pull down on the plastic filter bowls to remove them from the upper filter housing taking care to remove the O-rings. The O-rings can be discarded.
- The black filter element on the left can be removed from the upper filter housing by rotating clockwise and discarded.
- The white filter element on the right can be removed from the plastic filter bowl by gently prying up on the black upper filter assembly with the O-ring removed. Once removed from the filter bowl, rotate the lower piece of the filter assembly a quarter turn counter clockwise. The white element can be discarded and replaced and then reassembled.
- Fill the plastic filter bowl about half way with warm soapy water and shake with your hand covering the top opening. Repeat for both bowls. This will ensure that the float drain is clean and operational.
- Remove and replace the O-rings on the lip of the plastic filter bowl.
- Install the outer metal casing back onto the plastic filter bowl, taking care to line up the protrusion on the bottom with the opening in the metal casing.
- Reinstall the filter housing and casing back into the upper filter assembly. Only tighten hand tight and do not use a wrench.
- Reinstall the poly drain lines by pushing up into the bowl until the push to connect fitting locks the line into place.
- The compressor intake filter can be replaced by pushing down on the black filter bowl located on the top of the compressor and rotating counter clockwise. Take care that the filter housing may be hot.
- Turn on the unit and test for any leaks with a a spray bottle and soapy water.
- Reset the filter alarm by holding the Down (-) key on the controller for 10-15 seconds.
- Power down the unit and confirm that the pressure reading on the gauge above the filters reads 0 PSI.
- Disconnect the drain lines from the filter bowls by pushing the orange rings towards the filter bowl, while pulling down on the poly lines.
- Unscrew the filter bowls by hand by rotating the outer metal casing clockwise.
- Pull down on the plastic filter bowls to remove them from the upper filter housing taking care to remove the O-rings. The O-rings can be discarded.
- The black filter element on the left can be removed from the upper filter housing by rotating clockwise and discarded.
- The white filter element on the right can be removed from the plastic filter bowl by gently prying up on the black upper filter assembly with the O-ring removed. Once removed from the filter bowl, rotate the lower piece of the filter assembly a quarter turn counter clockwise. The white element can be discarded and replaced and then reassembled.
- Fill the plastic filter bowl about half way with warm soapy water and shake with your hand covering the top opening. Repeat for both bowls. This will ensure that the float drain is clean and operational.
- Remove and replace the O-rings on the lip of the plastic filter bowl.
- Install the outer metal casing back onto the plastic filter bowl, taking care to line up the protrusion on the bottom with the opening in the metal casing.
- Reinstall the filter housing and casing back into the upper filter assembly. Only tighten hand tight and do not use a wrench.
- Reinstall the poly drain lines by pushing up into the bowl until the push to connect fitting locks the line into place.
- The compressor intake filter can be replaced by pushing down on the black filter bowl located on the top of the compressor and rotating counter clockwise. Take care that the filter housing may be hot.
- Turn on the unit and test for any leaks with a a spray bottle and soapy water.
- Reset the filter alarm by holding the Down (-) key on the controller for 10-15 seconds.
BeerBlast Beverage Grade Nitrogen Generators
Sizing consideration: factor in peak performance days, such as Superbowl Sunday or New Year’s Eve.
Image
Models
Description
Datasheets
Request a quote
Model
3KPH
Description
* 5.2 SCFH Nitrogen production
* Max pints/min: 24
* Wall or tank mount options
* BlastOff Leak Detection System
* Available with or without Blender
* Only available in US
Datasheets
Model
7KPH
Description
* 14 SCFH Nitrogen production
* Max pints/min: 40
* Wall or tank mount options
* BlastOff Leak Detection System
* Available with or without Blender
Datasheets
Model
14KPH
Description
* 24 SCFH Nitrogen production
* Max pints/min: 50
* Floor Mounted
* BlastOff Leak Detection System
* Available with or without Blender
Datasheets
- Download
- Flow rates dependent on nitrogen purity and pressure specifications.
- Flow rates dependent on nitrogen purity and pressure specifications.
- Flow rates dependent on nitrogen purity and pressure specifications.
- Flow rates dependent on nitrogen purity and pressure specifications.
- Food & Beverage
Beer Blast
Mission-Critical Nitrogen™ BeerBlast Mixed Gas Dispense System
The BrewBlast Nitro Gas Dispense System is designed specifically for mission-critical nitrogen™ infused cold brew coffee applications. Engineered with the most efficient nitrogen gas separation technology and the smallest available footprint, BrewBlast produces ultra-pure nitrogen gas for pouring cold brew coffee. Generate nitrogen on-demand and ensure your cold brew tastes just as the brewer intended.
- Industrial Metals
N2GEN: Mission-Critical Nitrogen™ Generators for Heat-Treating Processes
For years, the heat treating industry has depended on the inert properties of nitrogen to push oxygen out of high-temperature environments, often requiring high flowrates and purities in a short amount of time. South-Tek Systems’ mission-critical nitrogen™ generators are engineered to reliably deliver the exact purity and flowrate your Heat-Treating process requires.
South Tek’s industrial N2GEN system uses dual-bed, PSA technology. The PSA (Pressure Swing Adsorption) filtration delivers 99.999% pure nitrogen while the dual-bed design allows for maximum efficiency and minimal maintenance. Combined, the dual-bed design and PSA technology are a powerful solution with an 18-24 year system life dependent on maintenance.
In addition to hassle-free, in-house mission-critical nitrogen™ generation, clients benefit from significant cost savings of 50-90% on average and quick payback with a typical ROI of around one year. South-Tek offers rental, lease and purchase options – all of which provide savings.
- Flow rates dependent on nitrogen purity and pressure specifications.
N2Blast
N2Blast: Mission-Critical Nitrogen™ Generators for Dry Fire Protection Systems
The N2Blast Corrosion Inhibiting System is designed to protect fire protection sprinkler systems from corrosion and extend system life. The N2Blast nitrogen generator introduces up to 98.5%+ pure nitrogen into the dry or pre-action fire protection system and displaces oxygen, a key contributor to the corrosion reaction, using the AutoPurge System. The N2Blast effectively inhibits Electrochemical, Galvanic and Microbiologically Influenced Corrosion (MIC), as well as sprinkler pipe ice plugs.
N2GEN
N2GEN: Mission-Critical Nitrogen™ Generators for Laser Cutting
Minimize Beer Waste, Maximize Profit
Over- and under-carbonation can affect the quality and taste of beer. In addition, they both lead to a loss in revenue and customer satisfaction. The BeerBlast System helps establishments provide the highest quality beer, while minimizing waste and recuperating revenue loss.
Over-carbonation can occur when pushing beer with either 100% CO2 or an incorrect mixed gas ratio. This can result in a “foamy pour” which will either leave the customer unsatisfied with their pint or the bartender will continue to pour the foam out and refill the glass until the desired level of foam is reached. Even worse, the wrong blend can actually ruin the contents in the keg. Up to 20% of the beer that should be sold to customers will turn to foam and remain in the keg when it heads back to the wholesaler!
On the other hand, under-carbonation results in over-pouring and flat, foul tasting beer. Instead of a nice foam head to preserve the flavors of the beer, the customer will be met with no foam on the top. This may seem ideal, but the flavor profile of the beer will be completely different than the brewer intended. Also, the establishment will be over pouring each pint by about ~20% more beer leading to much smaller profit margins.
South-Tek’s mission-critical nitrogen™ BeerBlast system eliminates over- and under-carbonation to ensure you pour as many salable pints as possible from each keg. Below is a conservative example of profit loss for a mid-sized restaurant/pub:
Product Loss | |
---|---|
Beer wasted per month | $600.00 |
Kegs consumed per month | 60 |
Average cost per keg | $100.00 |
Beer loss per keg | 10% |
Revenue Loss | |
---|---|
Revenue loss per month | $3,720.00 |
Kegs consumed per month | 60 |
Pints per keg | 124 |
Sell price per pint | $5.00 |
Beer loss per keg | 10% |
- Food & Beverage
Mission-Critical Nitrogen™ BrewBlast Nitro Gas Dispense System
The BrewBlast Nitro Gas Dispense System is designed specifically for mission-critical nitrogen™ infused cold brew coffee applications. Engineered with the most efficient nitrogen gas separation technology and the smallest available footprint, BrewBlast produces ultra-pure nitrogen gas for pouring cold brew coffee. Generate nitrogen on-demand and ensure your cold brew tastes just as the brewer intended.
- Fire Protection
N2Blast: Mission-Critical Nitrogen™ Generators for Dry Fire Protection Systems
The N2Blast Corrosion Inhibiting System is designed to protect fire protection sprinkler systems from corrosion and extend system life. The N2Blast nitrogen generator introduces up to 98.5%+ pure nitrogen into the dry or pre-action fire protection system and displaces oxygen, a key contributor to the corrosion reaction, using the AutoPurge System. The N2Blast effectively inhibits Electrochemical, Galvanic and Microbiologically Influenced Corrosion (MIC), as well as sprinkler pipe ice plugs.
- Industrial Metals
N2GEN: Mission-Critical Nitrogen™ Generators for Laser Cutting
South-Tek Systems’ mission-critical nitrogen™ generator Laser Series is engineered to meet the various gas consumption needs of typical laser applications for all materials & thicknesses. Our dual-bed PSA (Pressure Swing Adsorption) filtration technology is the gold standard of nitrogen generation and ensures a reliable source of clean, dry, particulate-free nitrogen supply on demand.
Our mission-critical nitrogen™ generation solutions cater to the laser-cutting industry’s specific needs. Whether your nitrogen needs are for high production fabrication or you need flexible storage for cutting varying material types and thickness – South-Tek offers a standard product line engineered to meet your specific needs.
Mission-Critical Nitrogen™ BlastOff – Leak Detection System
Provided exclusively with BlastOff – Leak Detection System, BeerBlast is designed to detect beer gas leaks before they become catastrophic. This nitrogen generator technology helps reduce service call expenses, gas run-outs, and protects the asset from unnecessary (excessive) operating hours.
- Minimizes risk of hazardous gas build up in keg box
- Eliminates untimely nitrogen gas runouts
- Ensures kegs are properly tapped
- Maximizes lifespan of the BeerBlast
Subscribe to the South-Tek Newsletter!
Stay up-to-date with the latest news and exclusive offers by subscribing to our newsletter today!
Subscribe to the South-Tek Newsletter!
Stay up-to-date with the latest news and exclusive offers by subscribing to our newsletter today!
South-Tek Systems Team
The entire South-Tek Systems team takes pride in delivering superior products to our clients.
Sales
Engineering
Production & Quality
Service
Executive Leadership
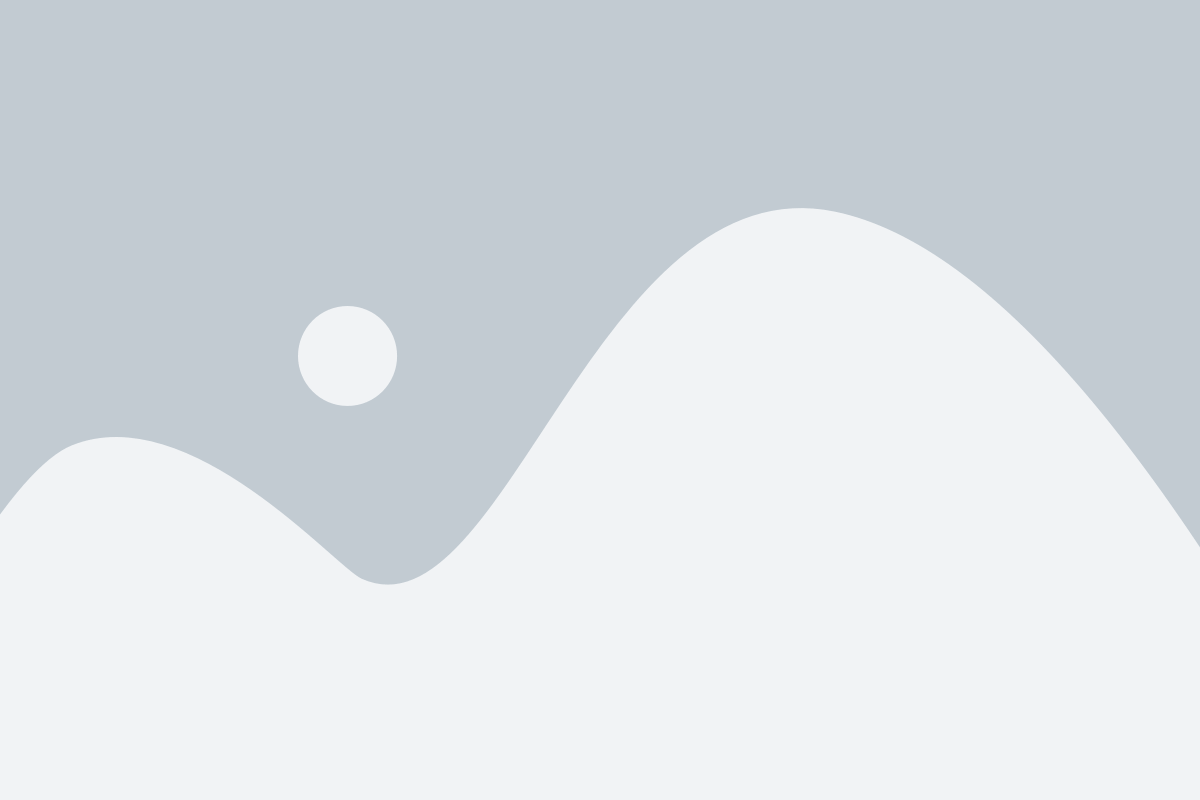
First & Last name
Position
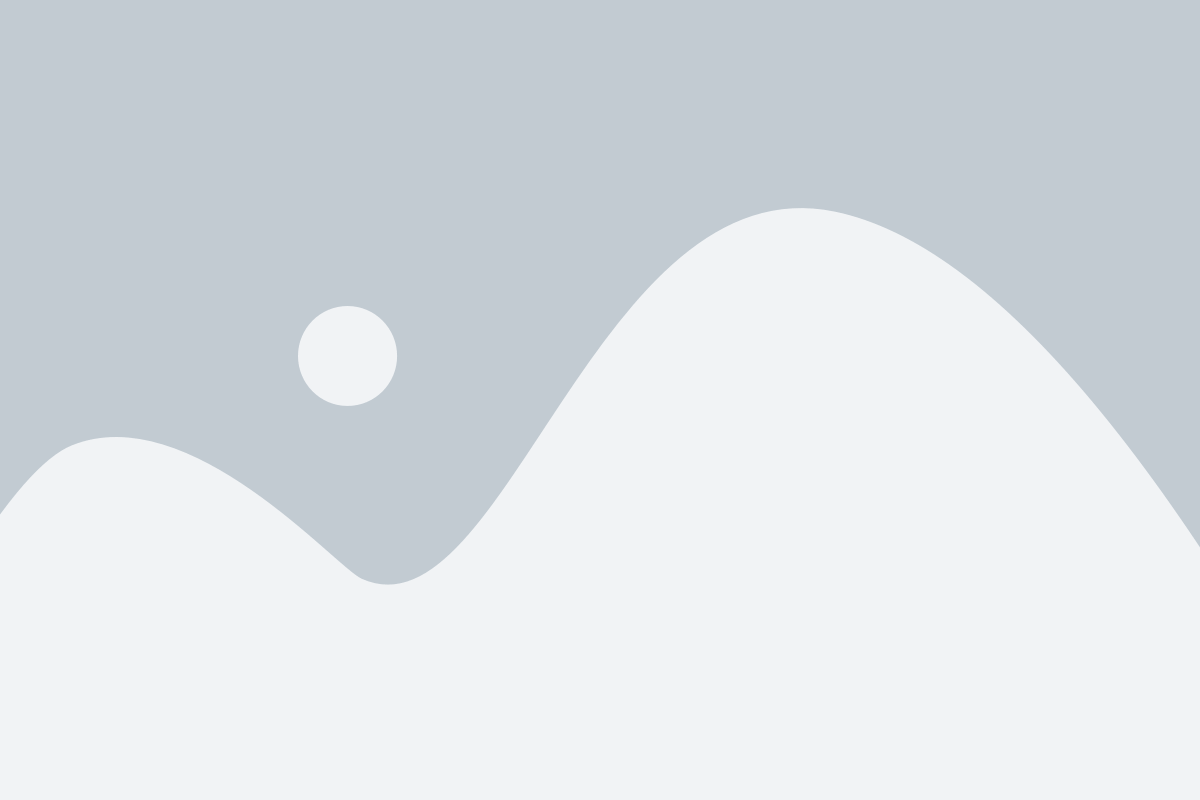
First & Last name
Position
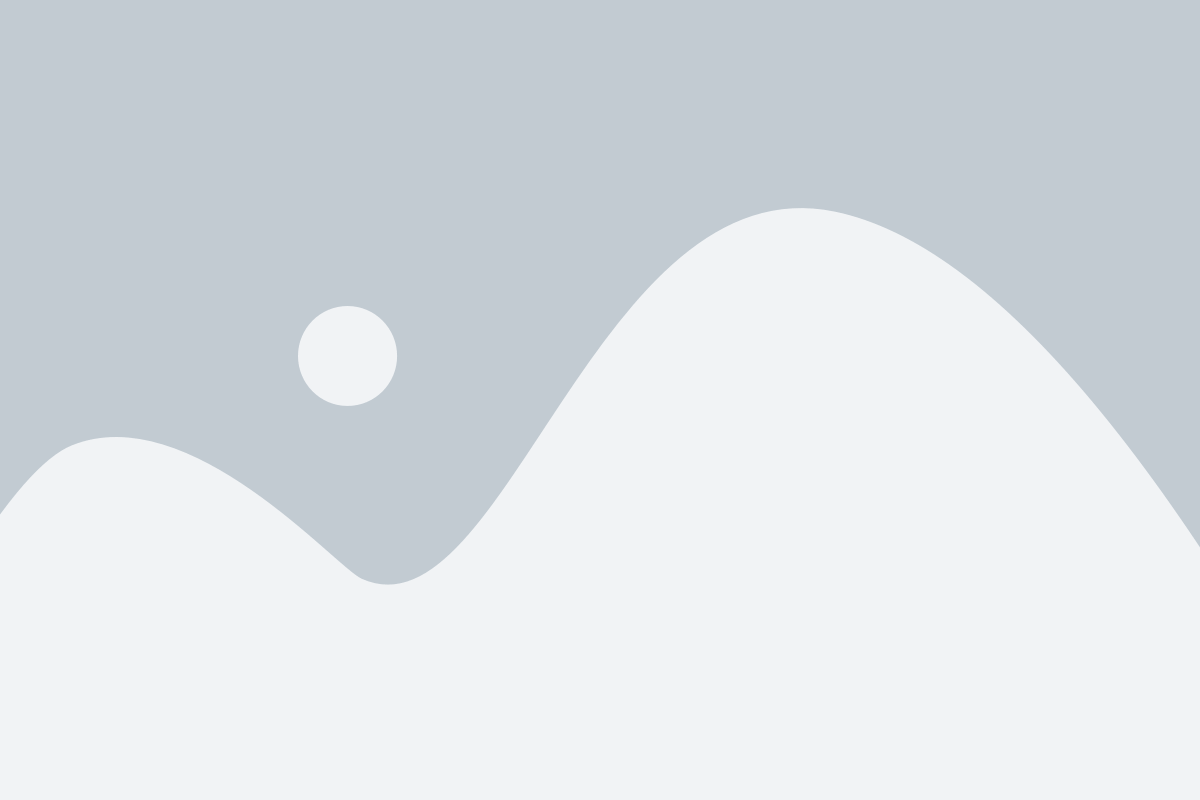